Principales causas de fallo de los sistemas de control PLC
PLC es el acrónimo de controlador lógico programable. Un PLC traduce las comas para que las máquinas las entiendan. Sin PLC, las acciones que los humanos desean que realicen las máquinas serían imposibles de descifrar para la máquina. El PLC traduce la información que una persona proporciona a una máquina, como pulsar un botón, y la convierte en un código que dirige a la máquina hacia la orden que se le ha dado. Los PLC se desarrollaron por primera vez a finales de la década de 1960 y no han hecho más que volverse más complejos e intrincados. Los PLC son la razón por la que las máquinas pueden completar tareas específicas. Hay algunos problemas que aún persisten en los PLC, y se desarrollan más a medida que la codificación se hace más compleja. Cuando el PLC falla en una máquina, ésta ya no puede interpretar las tareas que debe realizar y, por lo tanto, deja de funcionar con normalidad. Esto puede ser perjudicial para una operación en aplicaciones industriales, ya que causará grandes cantidades de tiempo de inactividad no programado. Descubra las principales causas de fallo del sistema de control PLC para proteger mejor sus instalaciones.
Fallo del módulo de entrada/salida
Ésta es la razón más común de los fallos de los PLC. Un signo revelador de un fallo del sistema PLC de entrada/salida es una parada repentina del proceso o un funcionamiento irregular. Esto se debe a que el sistema de control PLC está esperando una señal que lo guíe a través de una secuencia programada, pero la señal no es capaz de llegar correctamente.
Cuando esto ocurre, un ingeniero debe determinar dónde se detuvo originalmente la secuencia. Esto se suele hacer mediante una exploración del software para rastrear el problema hasta un punto específico del módulo de entrada/salida.
Una vez identificado el punto de entrada/salida, el ingeniero puede seguir el problema hasta la causa original. Esto suele incluir errores de configuración del PLC, disyuntores triples, fallos en los suministros de VCC, problemas con los cables o incluso un bloque de terminales suelto. Para solucionarlo, el ingeniero necesitará tener a mano piezas de repuesto.
El objetivo de todo este proceso es encontrar la desconexión entre la situación interna, que es lo que el PLC está "pensando" o interpretando, y la situación externa, o lo que está ocurriendo en realidad.
Interferencias por ruido eléctrico
Las interferencias de ruido eléctrico pueden tener un gran impacto en el sistema de control PlC. Esto ocurre típicamente cuando hay interferencia de señal extraña de interferencia electromagnética o interferencia de radiofrecuencia.
Para evitar interferencias de ruido eléctrico, asegúrese de almacenar cualquier motor grande o máquina similar lejos del sistema PLC. El riesgo de que esto ocurra también aumenta durante las tormentas eléctricas. Otras causas de interferencia de ruido eléctrico incluyen antenas y transmisores portátiles que se utilizan cerca de un PLC. Esto crea interferencias de radiofrecuencia. Cualquiera de estos problemas puede dar lugar a daños extremos que son costosos de reparar. Lo ideal es evitar por completo las interferencias de ruido eléctrico. Discutir las posibles opciones con un ingeniero cualificado es el mejor método para prevenir fallos en el sistema de control PLC debidos a interferencias de ruido eléctrico.
Problemas de alimentación
Los problemas de alimentación eléctrica también son causas comunes de fallos en los sistemas de control PLC. Los sistemas de control PLC necesitan un flujo constante de energía o electricidad para funcionar según lo previsto. Cuando la energía se pierde o fluctúa, el PLC ya no puede funcionar correctamente, y estas interrupciones frecuentes pueden causar un fallo completo del sistema. Los problemas de suministro eléctrico pueden deberse a pérdidas de energía, apagones, fallos de la red, cables viejos o deshilachados, conexiones sueltas u otros problemas eléctricos comunes. Aunque muchas de estas cosas son prácticamente inevitables, hay algunas maneras de proteger sus sistemas de control PLC, ya que la pérdida frecuente de energía puede conmocionar el sistema y causar una gran pérdida de datos que es difícil y costosa de reparar.
Algunos de los métodos para evitarlo incluyen la instalación de una fuente de alimentación de reserva diseñada para activarse cuando la fuente de alimentación principal falle o experimente roturas. Otro método es hacer que un ingeniero eléctrico cualificado inspeccione y planifique para el futuro. Además, los ingenieros pueden mantener baterías en sus sistemas PLC. Estas baterías ayudan a mantener el sistema en funcionamiento durante cortos periodos de tiempo entre pequeños cortes y problemas.
Cuestiones de comunicación
Los sistemas de control PLC requieren una comunicación constante con los dispositivos circundantes y conectados. Cuando la comunicación falla, los dispositivos no serán capaces de entender sus tareas requeridas ya que el sistema PLC no será capaz de comunicarse eficazmente con ellos. Esta comunicación suele facilitarse a través de cables Ethernet con conexiones estables y seguras.
Para evitar estos problemas, los sistemas PLC deben inspeccionarse periódicamente y recibir un mantenimiento regular. Esto debe realizarlo un ingeniero cualificado que pueda garantizar que la red de comunicación está instalada correctamente y que todos los dispositivos conectados envían señales correctas a los demás.
Los problemas de comunicación pueden provocar grandes periodos de inactividad en las instalaciones que dependen de sistemas de control PLC.
Memoria dañada
Otros factores externos del sistema de control PLC también pueden causar una memoria corrupta. Cuando la memoria de un sistema de control PLC se corrompe, el código del PLC puede volverse ilegible, lo que puede causar un apagado involuntario. Cuando se produce este problema, no hay una solución fácil si no hay una copia de seguridad de la información y los datos en un dispositivo de almacenamiento. Para evitar un fallo total, lo mejor es guardar una copia de los datos en un dispositivo que esté almacenado en un lugar seguro y alejado de posibles interferencias, temperaturas extremas y cualquier tipo de humedad.
Hay muchas causas principales de fallo del sistema de control PLC a tener en cuenta en una operación. Póngase en contacto con Dreiym Engineering hoy mismo para realizar un estudio de análisis de carga eléctrica. En estos estudios, nuestros profesionales nace cp4-Los ingenieros certificados realizan un estudio del sistema de distribución eléctrica de sus instalaciones para determinar el equilibrio o desequilibrio del sistema. A continuación, podemos realizar una evaluación de la carga eléctrica, empezando por la creación de listas de carga eléctrica y perfiles de carga crítica. A continuación, analizamos la capacidad de sus instalaciones y las provisiones disponibles para el crecimiento futuro, de modo que podamos solucionar los problemas de los sistemas sobrecargados, tanto ahora como en el futuro.
Póngase en contacto con nosotros hoy mismo para realizar un análisis de la carga eléctrica de sus instalaciones o incluso de su hogar si está experimentando problemas de facturación, consumo eléctrico u otros problemas relacionados con la electricidad. Nuestro objetivo es adaptar su experiencia a sus necesidades, no solo para identificar y resolver los problemas actuales, sino también para planificar el futuro y evitar problemas.
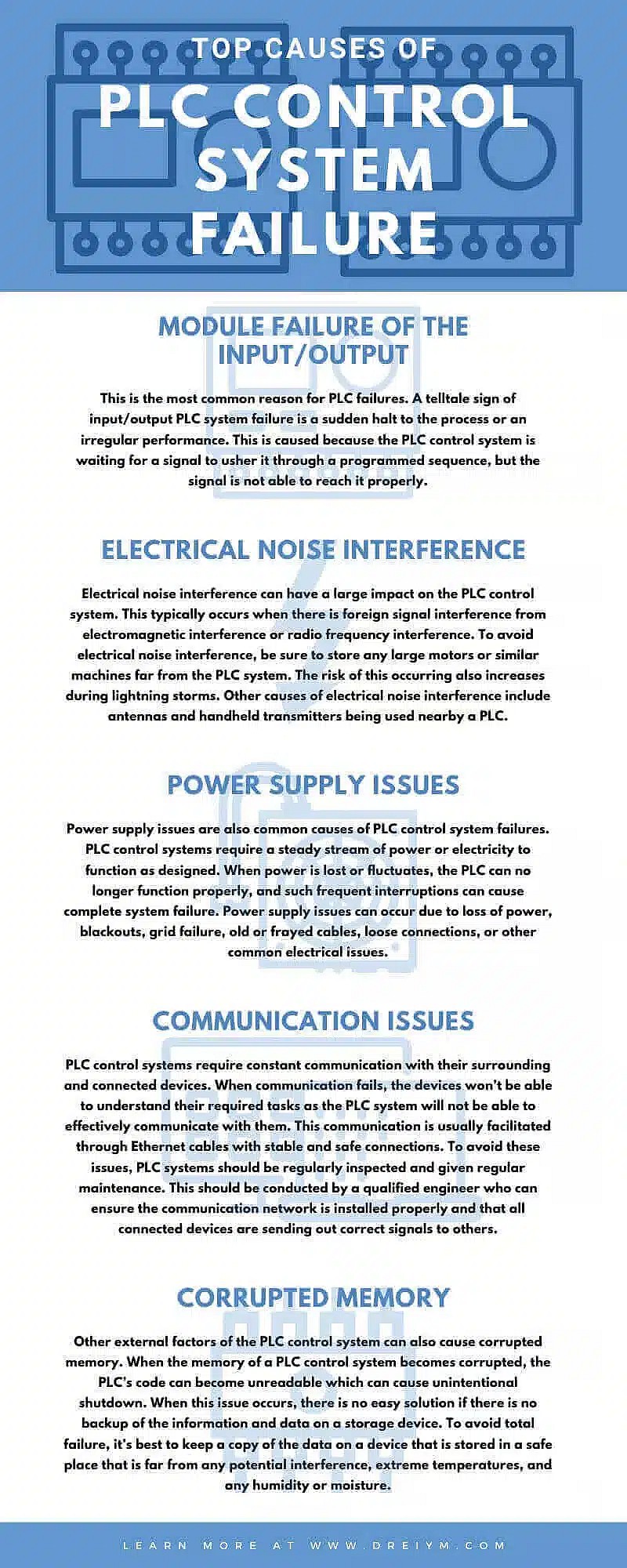